NCKU Team Develops Ultra-Fine Stainless Steel Wire to Propel Semiconductor Industry into New Era
Professor Hung's team has been specializing in metal material research for more than 20 years. In 2023, they successfully developed innovative heat-resistant duplex stainless steel wire materials in collaboration with Taiwan's special steel manufacturer, Walsin Lihwa. The steel wire, pulled by Hong Kong's Nichetech Co., Ltd., achieved a record-breaking thickness of only 30 micrometers (one millionth of a meter). This year, the team further developed multi-stage annealing (vacuum high-temperature softening) technology, successfully challenging 15 micrometers, reaching the level suitable for use in semiconductor electronic packaging wire bonding, not only innovating records again but also becoming a new benchmark in the world's wire technology.
Professor Hung stated that as chips become smaller, ultra-fine metal wires must be used for conduction. In the past, gold wires were used because of their excellent ductility, which could be drawn into 15-micrometer filaments. However, the cost was too high. The current market mainstream is to replace gold with copper, but copper has the problem of rusting, requiring high-specification packaging to avoid environmental influences, or to use gold-plated copper wires. However, electroplating is a highly polluting process with difficult subsequent treatment.
With the efforts of graduate students Yi-Ze Zhang and Chung-Kai Hsu from the Department of Materials Science, the team successfully welded 15-micrometer stainless steel wires to commonly used aluminum and copper substrates in semiconductors to complete wire bonding into balls. Through electrical analysis, it was confirmed that the resistance of the ultra-fine stainless steel wire was similar to that of copper wires and could be replaced. Welding steel balls on copper pads can be said to be an industry innovation, with a combination of strength and low interface resistance characteristics, meeting the requirements of semiconductor electronic packaging applications.
Professor Hung expressed that in the past, no one in the industry had thought that stainless steel could be drawn into such thin filaments and used on chips. Currently, copper costs about 200 to 300 yuan per kilogram, while stainless steel is only half that price. Not only is the cost lower, but there is also no rust problem. It can reduce packaging specifications and save even more, making it the star of semiconductor material applications.
Team members, graduate students Jian-De Huang and Che-Wei Lu from the Department of Materials Science, used 30-micrometer heat-resistant stainless steel wires to make probe springs, commissioned by Tainan's HCHI Industrial Co., Ltd. Due to their many advantages, they have attracted the attention of the international giant Smiths Interconnect. Senior executives of the company specifically came to Taiwan to obtain the new product, which is currently being tested in the UK.
Professor Hung stated that after the production of high-end chips, they need to rely on probe testing for conductivity. If they fail, they are removed. The extremely fine probes are equipped with springs. Currently, the probe springs used in the semiconductor industry are mainly made of 304 stainless steel. Although it is soft and can be drawn into fine wires, the disadvantage is that it is not heat-resistant. When tested with electricity, it often has a lifespan of only 2 to 3 days on the production line, losing elasticity and needing replacement. A set of probes often costs tens of thousands of yuan, and after replacement, it takes several hours to adjust, which is costly and time-consuming.
He said that probe springs made of heat-resistant stainless steel wires can withstand temperatures above 700 degrees Celsius, increasing the lifespan by 4 to 5 times compared to traditional springs. At the same time, because 304 stainless steel is not heat-resistant, it cannot withstand rapid electrification and can only be used at low currents. Testing speed is slow. Using new springs can quickly complete the test, and the new product is a major contribution to the manufacturing of AI chips.
Professor Hung's team has made great breakthroughs in semiconductor materials, which has greatly excited the industry. Professor Hung stated that the two achievements are ahead of the industry, and the ultra-fine stainless steel wire has entered the field of semiconductor technology, helping the semiconductor industry enter a new era. More tests will be conducted, and the team will continue to develop more applications for stainless steel materials in the future.
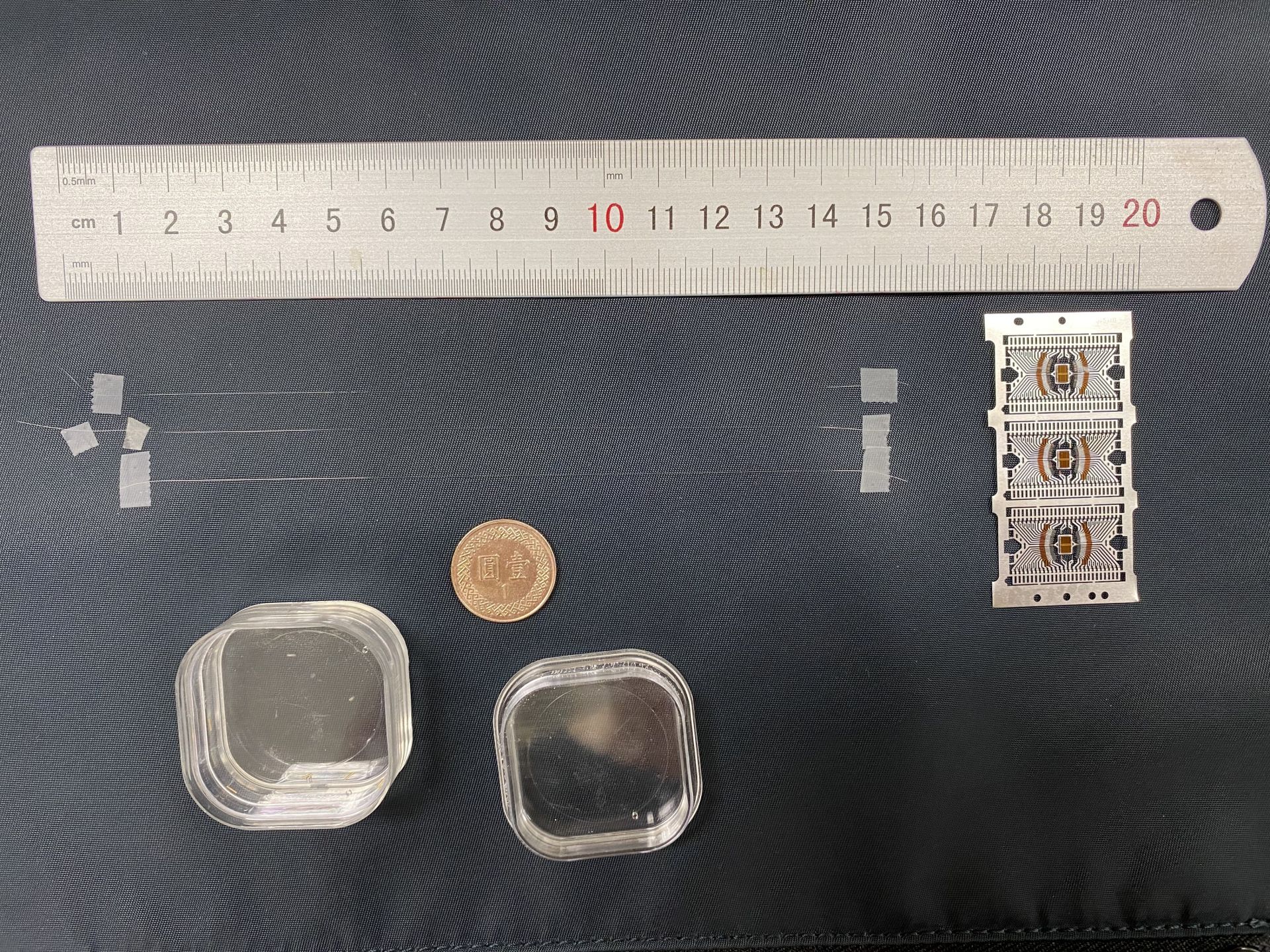
Professor Fei-Yi Hung's team from the Department of Materials Science at NCKU has developed ultra-fine heat-resistant stainless steel wires, ushering in a new era for the semiconductor industry.
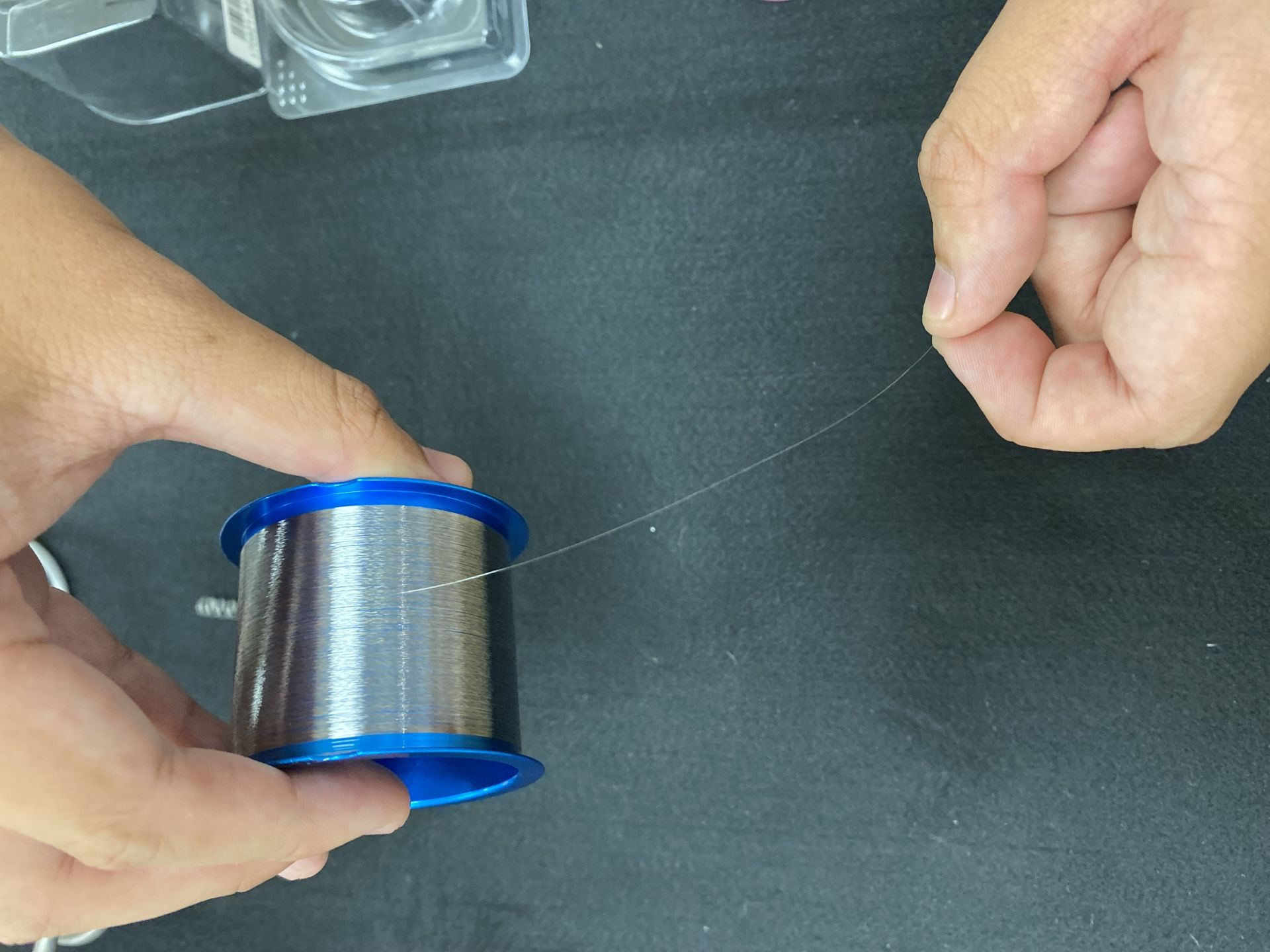
Professor Fei-Yi Hung's team from the Department of Materials Science at NCKU has employed innovative technology to draw heat-resistant stainless steel into wires as fine as only 15 micrometers.
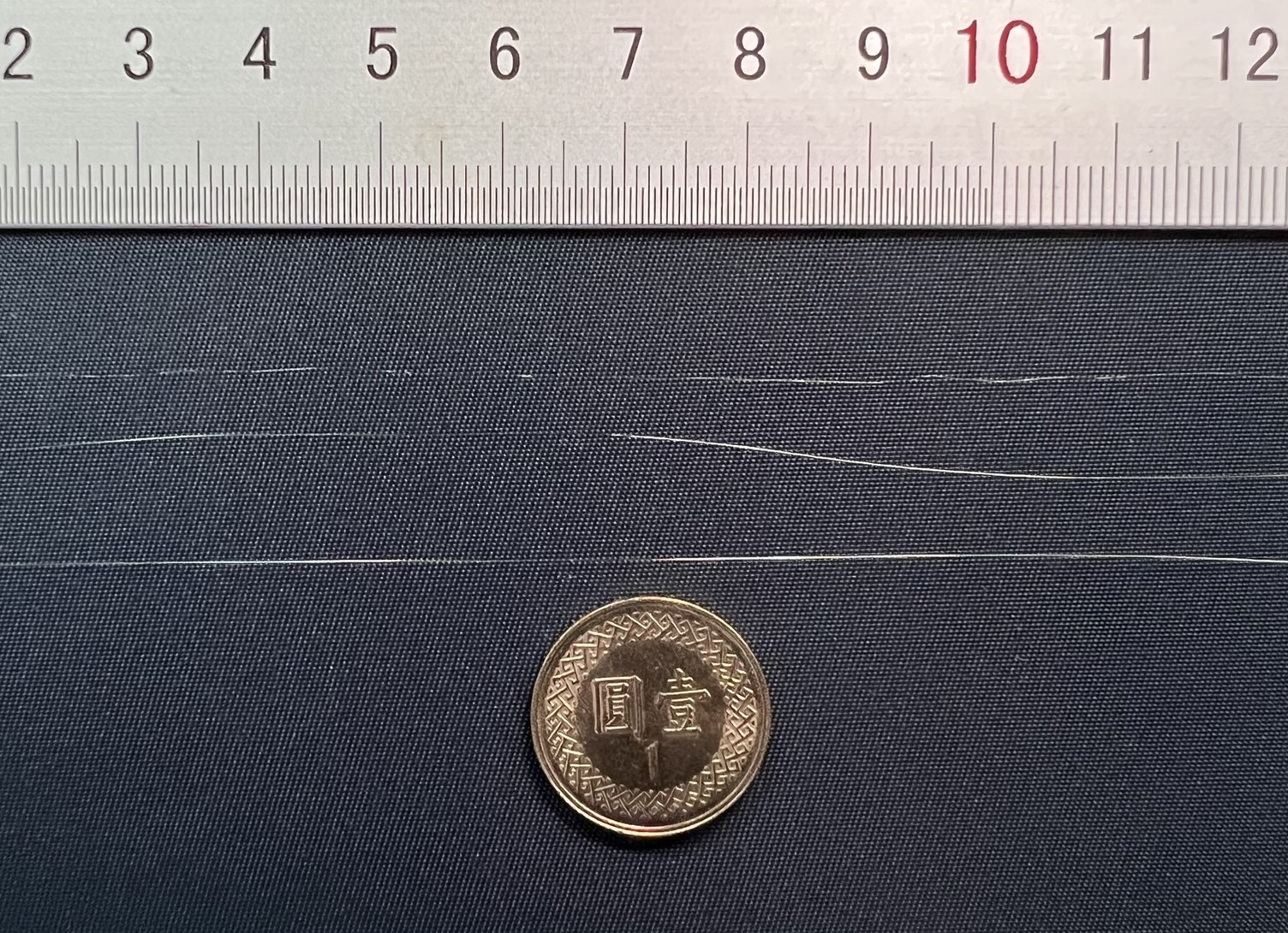
Professor Fei-Yi Hung's team from the Department of Materials Science at NCKU has utilized innovative technology to draw heat-resistant stainless steel into wires as fine as 15 micrometers.
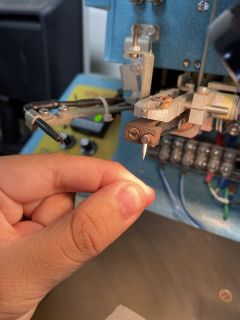
Professor Fei-Yi Hung's team, a group of specially appointed professors in the Department of Materials Science at NCKU, has successfully welded 15-micrometer stainless steel microwires onto commonly used aluminum and copper substrates in semiconductor applications, completing the wire bonding process into spherical shapes.
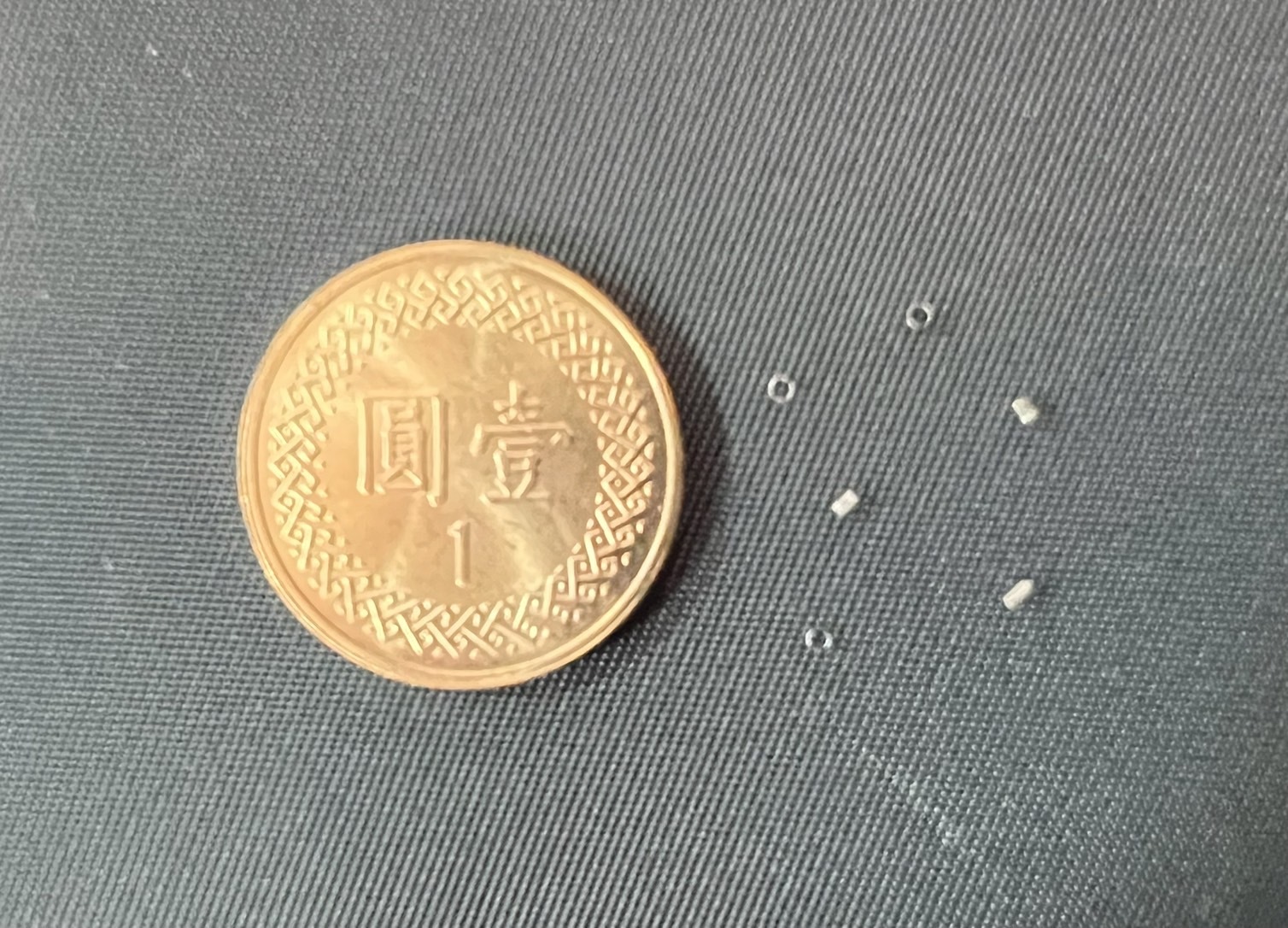
Professor Fei-Yi Hung's team, a group of specially appointed professors in the Department of Materials Science at NCKU, has utilized innovative technology to produce probe springs required for testing high-end chips using 30-micrometer heat-resistant stainless steel microwires.